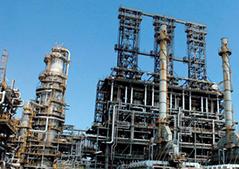
Совершенствование процесса переработки сырой нефти с каждым годом требует внедрения все более современных технологий и применения высокотехнологичных приборов и решений.
В процессах переработки нефти можно выделить несколько основных этапов: подготовку к переработке (обессоливание), первичная переработка с разделением нефти на фракции по температурам кипения; последующая вторичная переработка получившихся фракций и выработка компонентов нефтепродуктов; финальная стадия по смешению готовых продуктов для получения продукции заданного качества.
Содержание солей в сырой нефти довольно велико, поэтому перед переработкой она поступает на электрообессоливающую установку ЭЛОУ. Там происходит смешивание нефти с водой с последующим разделением с помощью высокого напряжения (до 30кВ). Для повышения эффективности данного процесса в современных производствах производят дозирование дополнительных веществ — деэмульгаторов. Это специальным образом подготовленная смесь поверхносто-активных веществ в углеводородном растворителе, которая подается на этапе закачки сырой нефти в ЭЛОУ и обеспечивает предотвращение образования эмульсии и разрушение уже существующих.
После обессоливания нефтяная эмульсия поступает в атмосферно-вакуумную трубчатку (АВТ), в которой происходит первичная переработка нефти. Здесь происходит нагрев сырья в ректификационной колонне, состоящей из нескольких десятков отборных устройств (тарелок). Поскольку различные компоненты нефти выкипают при разных температурах, то в разных частях ректификационной колонны отводятся различные нефтяные фракции от бензиновой и дизельной (сверху) до мазутной (снизу) см. рисунок.
При нагревании нефтяные фракции не разлагается полностью и требуют дальнейшей переработки. Чем эффективнее и технологичнее процесс переработки, тем более чистые фракций можно получить, а также снизить потребление топлива для нужд производства и количество отходов в виде мазута. В совокупности это называют показателем глубины переработки нефти, выражающейся в процентах полученных товарных продуктов от общего количества переработанной нефти. В России на 2016 год эта величина едва превышает 70%, в то время как в развитых странах Европы, а также США это примерно 90% и выше.
Для контроля и поддержания значений pH среды внутри ректификационных колонн и установок первичной переработки нефти используют такие реагенты как нейтрализаторы. Получают такие вещества из аминогрупп, смешанных в воде или ароматических растворителях. Дозирование этого реагента позволяют снижать активность кислых компонентов в конечных продуктах, тем самым повышая их качество.
Также существует проблема высокого содержания в нефти серы, которая придает конечным продуктам неприятный запах, а в соединениях с водой приводит к повышенной коррозии металла. Частично решить эту проблему помогает использование специальных ингибиторов коррозии, которые дозируются непосредственно в ректификационную колонну через специальные форсунки, расположенные вдоль всей высоты. Ингибиторы коррозии получают смешиванием аминных групп и их производных. Их использование позволяет значительно снизить скорость коррозии материалов колоны, трубопроводов и прочего оборудования путем образования на поверхности металла защитной пленки.
Компания Сигм плюс инжиниринг совместно с заводом Кортем-Горэлтех и компанией Bronkhorst (Нидерланды) готова предложить универсальное и комплексное решение задач дозирования нейтрализаторов, деэмульгаторов и ингибиторов коррозии в любом технологическом процессе, связанном с переработкой нефти. Система представляет собой измеритель расхода, соединенный с регулирующим клапаном. При этом происходит одновременное измерение реального потока жидкости и его регулирование, т.е. поддержание на заданном уровне. Система является высокотехнологичным продуктом, позволяющим измерять и регулировать расход с высокой точностью. При этом ее компактные размеры, стоимость и сроки поставки являются значительными преимуществами перед аналогичными системами на рынке. Выбор моделей с диапазонами дозирования от 5г/ч и до 300 кг/ч позволяет внедрить наш продукт как на крупнейшие нефтеперерабатывающие заводы России, так и в небольшие цеха по получению конечных продуктов нефтепереработки. При этом один и тот же прибор может использоваться сразу с несколькими типами реагентов, поскольку показания прибора не зависят от температуры, плотности и теплопроводности. При этом нет необходимости производить повторную калибровку, так как показания автоматически пересчитываются внутри прибора и выдаются оператору на АСУ-ТП. Наше решение имеет все необходимые сертификаты и соответствует всем требованиям Технического регламента Таможенного союза ТР ТС 012/2011 «О безопасности оборудования для работы во взрывоопасных средах», может эксплуатироваться при температуре окружающей среды от −60°С до +40°С, может эксплуатироваться 24 часа в сутки 365 дней в году, а срок службы составляет до 25 лет.
Для подбора требуемого Вам оборудования Вы можете обратиться в компанию Сигм плюс инжиниринг, где опытные специалисты проконсультируют Вас о моделях необходимого оборудования, этапах его внедрения и возможностях его подключения к имеющейся архитектуре АСУ-ТП.